Lagerhaltungskosten reduzieren – Maßnahmen und Tipps
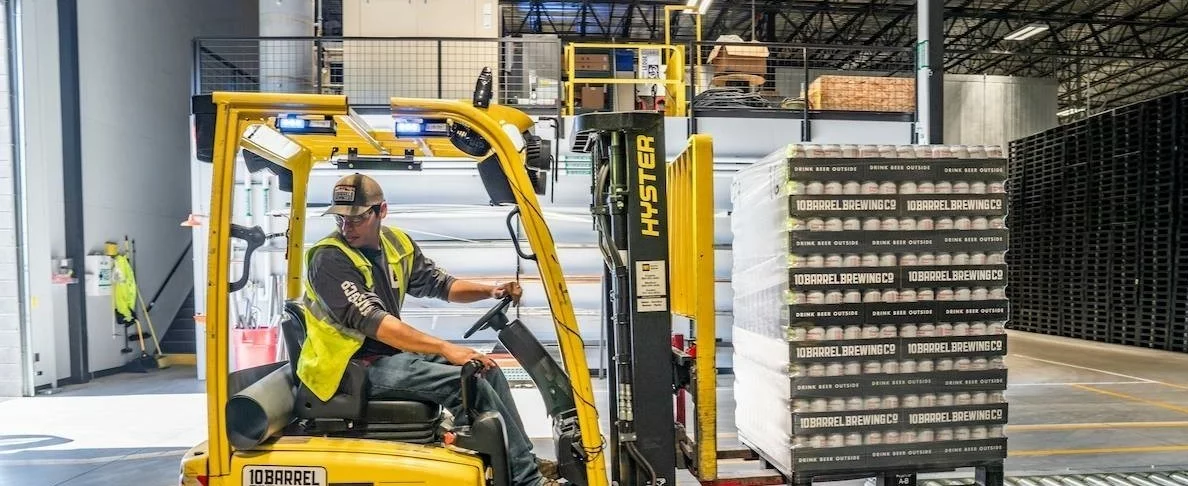
Lagerhaltungskosten stellen Kosten dar, die während der Lagerung von Roh-, Hilfs- und Betriebsstoffen sowie während des Produktionsprozesses entstehen. Aber auch bei der Lagerung von Fertigerzeugnissen, die bis zum Verkauf im Lager verbleiben müssen, entstehen Kosten. Bei diesem Vorgang werden die Lagerkosten, aber auch die entgangenen Zinsgewinne aufgrund der Kapitalbindung, die durch den Lagerungsprozess entstehen, miteinbezogen. Um eine Transparenz sämtlicher Lagerhaltungskosten zu schaffen, werden nun die erfassbaren und sichtbaren Kosten unterteilt. Möchten Sie Ihre betrieblichen Lagerhaltungskosten korrekt und realitätsnah berechnen, sind die Kostenbereiche unbedingt vollständig zu erfassen. Dadurch können Sie diese relativ genau den einzelnen Produkten zuordnen.
Lagerhaltungskosten entstehen beispielsweise aufgrund einer Zeitüberbrückung von benötigten Lagergütern, die notwendig sind, um sich während eines Produktionsverfahrens mit den benötigten Produkten einzudecken. Somit wird Leerlauf während der Produktion vermieden. Ein Aspekt, der in die Lagerhaltungskosten mit einzubeziehen ist, wären beispielsweise auch vom Unternehmen unterschriebene Verträge aus denen gesetzliche Lieferverpflichtungen mit Bezug auf die Verfügbarkeit von Ersatzteilen oder festgesetzten Garantieansprüchen hervorgehen.
Besonders Unternehmen, die im internationalen Handel unterwegs sind, sollten unbedingt den juristischen Rahmen der betreffenden Länder beachten. Nicht selten können hierbei von Land zu Land horrende Schadensersatzansprüche entstehen. Dies käme durchaus zustande, befänden sich keine vertraglich vereinbarten Liefermengen im Lagerbestand. Dadurch würde der Kunde einen Ausfall seines Produktionsprozesses erleiden.
Welche Arten von Lagerhaltungskosten können entstehen?
Kosten der Lagerhaltung sind in vielen Betrieben eine unvermeidbare Kostensparte, die mit der Menge, der gelagerten Waren in direkter Verbindung steht. Der Großteil dieser Kosten besteht aus Sachkosten, der Personalkostenanteil ist relativ gering. Neben den direkt erfassbaren Kosten zählen auch die Kosten der Kapitalbindung. Lagerhaltungskosten werden aus ihren verschiedensten Bestandteilen heraus erfasst und berechnet. Alleine die zur Verfügung gestellten Räume, also die Kosten der Lagerkapazität und des Lagergebäudes selbst, sowie die anfallenden Kosten der Waren, zählen zu folgenden Faktoren hinzu.
Sämtliche Einrichtungsgegenstände angefangen von den Regalsystemen selbst, wie zum Beispiel die oft benutzten Hochregallager, schlagen ebenfalls mit Kosten zu Buche.
Einen Kostenfaktor stellen natürlich die Lagertransportmittel wie Gabelstapler oder Regalförderzeuge dar. Hier entstehen neben Reparaturkosten an den Geräten auch vereinzelt Kosten für Schulungen des betreffenden Personals. Um diese Gesamteinrichtung auch entsprechend nutzen zu können, ist der Einsatz von Lagerpersonal notwendig, das aufgrund seiner Ausbildung die angeforderte Tätigkeit kostengünstig und effektiv ausführen kann. Es steht außer Frage,
dass die gesamte Lagerbereitschaft, also die Lagerung selbst, die unter anderem Beleuchtungsmittel, Heizungs- oder Kühlkosten sowie deren Instandhaltungskosten mit einschließt, einen weiteren Kostenfaktor darstellt.
Letztendlich fallen Kosten für die quantitative sowie qualitative Erhaltung der Lagergüter an, wie beispielsweise Kosten für kalkulatorische Zinsen, die aufgrund des eingesetzten Kapitals zum Erwerb der Lagergüter entstand. Hohe Zinslasten haben aufgrund teurer Refinanzierungen oder plötzlich auftretenden erhöhten Zinssätzen eine erhebliche Bedeutung bei der Beschaffung von kapitalintensiven Gütern. Gerade in der Unterhaltungsbranche können Fernseher oder Computerausstattung einen großen Einfluss auf die Umsatzrendite bedeuten. Deshalb sind kalkulatorische Zinsen von den Waren- und Materialbeständen abhängig. Bei dem Versuch, den Aufwand der kalkulatorischen Zinskosten exakt auf die einzelnen Lagerbestände umzusetzen, sind aufwendige Berechnungen notwendig. Genau erfassen lassen sich die Kosten der Lagerung sowie deren Verrechnung, wenn man die zur Lagerverrichtung erbrachten Stellen als Kostenstelle oder Kostenplatz separiert sowie die Lagerleistungen genau aufzeichnet.
Wie sich Fixkosten sowie variablen Lagerhaltungskosten definieren
Als Lager-Fixkosten werden Kosten bezeichnet, die nicht von dem Beschäftigungsgrad oder der Produktionsmenge abhängen. Dennoch ergeben sich die Kosten der Lagerhaltung gemeinsam aus den fixen sowie variablen Kosten. Fixkosten sind in einem gewissen Zeitzyklus konstant und stehen nicht in einer Abhängigkeit von Produktions- oder Absatzmengen. Findet eine Erhöhung der Produktionsmenge statt, erhöht sich zwar der Materialeinsatz (variable Kosten), die Kosten für die sich im Gebrauch befindlichen Maschinen (fällt unter Abschreibung) jedoch nicht. Steht man einer zeitweisen Erhöhung von ehemals geringen Produktionsmengen verhalten gegenüber, so verändert sich dieser Aspekt bei einer deutlichen Erhöhung der Warenmenge und man spricht von sprungfixen Kosten.
Nehmen wir beispielsweise eine Verdoppelung der Warenmenge an, wobei die Maschine mit einer Kapazitätserhöhung von maximal 25 % bereits ausgelastet ist und deshalb der Kauf einer weiteren Maschine ansteht. Dieser Zukauf verursacht nun Fixkosten in Form von Abschreibung. Bei Fixkosten können sich die Stückkosten mit Höhe der Ausbringungsmenge verringern.
Variable Kosten hingegen verändern sich bei Änderungen von Produktions- oder Ausbringungsmenge, wodurch mengenabhängige Kosten entstehen. Diese Kostenveränderung kann sich wie folgt gestalten:
- Bei einer proportionalen Veränderung erhöhen sich mit jedem weiteren produzierten Stück die variablen Kosten im selben Verhältnis, wobei die Stückkosten gleich bleiben.
- Überproportional Veränderung würde bedeuten, dass sich mit jedem weiteren produzierten Stück auch die variablen Kosten pro Stück erhöhen.
- Unterproportionale Veränderung würde wiederum bedeuten, dass sich mit jedem weiteren produzierten Stück die variablen Kosten pro Stück vermindern.
- Die Unterscheidung von fixen und variablen Kosten hängt von der Ausbringungsmenge (Beschäftigung) ab.
Die Berechnung der Lagerkosten
Fast jeder Geschäftsbetrieb, seien es Produktionsstätten, Handelsbetriebe oder Shopbetreiber, verfügt über Lagerräume. Bei diesen Lagerungen entstehen Lagerkosten beziehungsweise Lagerhaltungskosten. Lagerkosten beinhalten sämtlich anfallende Kosten für Betriebs-, Hilfs- oder Rohstoffe, sogenannte Zwischenprodukte und Handelswaren. Auch Ersatzteile befinden sich unter anderem mit fertiggestellten oder teilweise produzierten Erzeugnissen in den Lagerräumen. Die Kosten, die durch die Lagerhaltung entstehen, beziehen sich auf die Kosten für Räumlichkeiten, Materialien und Personalkosten, sowie die Kapitalbindung durch Waren. Dabei können die Lagerungskosten in zwei Kostenblöcke unterteilt werden. Zum einen in die bereits erwähnten Lagerhaltungskosten und andererseits in die Zinskosten für das gebundene Kapital des Warenbestandes.
In der Regel erfolgt die Ermittlung der Lagerkosten jährlich über die Kostenstellenrechnung. Vorteilhaft zeigt sich hier die bereits getrennte Kostendarstellung über Kostenstellen. Miteinbezogen werden aufwandsungleiche Kosten d.h. kalkulatorischen Kosten, in Form von Abschreibungen, Miete oder Wagniskosten. Sollte keine Kostenstellenrechnung bestehen, ist es möglich, die Kosten aus der Gewinn- und Verlustrechnung oder Buchhaltung zu entnehmen und anteilig zu verrechnen. Sämtliche Lagerkosten bestehen dann allerdings nur aus aufwandsgleichen Kosten.
Ein wichtiges Instrument: Die Lagerkennzahlen bzw. Lagerkennziffern
Lagerkennziffern beziehungsweise Lagerkennzahlen gehören zu den statistischen Daten und dienen der Überprüfung zwecks Wirtschaftlichkeit der Lagerhaltung eines Betriebes. Die somit wichtigsten Lagerkennziffern bestehen aus Mindestbestand und Meldebestand sowie des durchschnittlichen Lagerbestandes, der Umschlaghäufigkeit und der durchschnittlichen Lagerdauer. Zur Berechnung des Lagerkostensatzes werden die Lagerkosten sowie der durchschnittliche Lagerwert herangezogen.
- Die Formel hierfür lautet: Lagerkostensatz = Lagerkosten/Durchschnitt Lagerwert *100
Mit der Lagerintensität liegt eine weitere wichtige Kennzahl im Bereich der Buchhaltung zugrunde. Besonders Branchen, die eine hohe Anzahl von Ersatzteilen oder vorgefertigten Teilen, die unter Umständen noch bearbeitet werden müssen, halten Vorräte im Lager. Dadurch werden Kapital gebunden und ebenso hohe Kosten verursacht. Um die Lagerintensität zu berechnen, benötigt man zwei Zahlen aus dem Jahresabschluss: das Vorratsvermögen (den Wert der Lagerbestände) sowie das Gesamtvermögen (entspricht der Bilanzsumme).
- Hierbei lautet die Formel: Lagerintensität = Vorratsvermögen/Gesamtvermögen *100
Erzielt man nun bei der Lagerintensität einen zu hohen Wert sollte dieser genau analysiert werden (Werte >130% erweisen sich als kritisch). Dahinter könnte möglicherweise ein fehlerhaftes Lagermanagement oder eine Steigerung der Produktionszeiten stecken. Auf jeden Fall stellt eine zu hohe Lagerintensität ein gewisses Risiko dar. Einmal steht hier der Preisverfall zur Debattes sowie der Verderb einer Ware oder deren Veralterung. Nicht zu vergessen sei die Kapitalbindung durch die Waren. Möchte man die Umschlaghäufigkeit berechnen, werden Lagerverbrauch sowie Lagerbestand miteinander ins Verhältnis gesetzt. Diese Kennzahl gibt beispielsweise an, in welchen Zeitabständen das Lager geleert sowie durch neue Warenbestände wieder gefüllt wird.
Lagerkosten reduzieren
Es gibt viele Gründe, die dafür sprechen, seine Lagerbestände zu reduzieren. Zum einen steckt eine teilweise viel zu hohe Kapitalbindung in den Warenbeständen, zum anderen kann durch eine Reduzierung der Warenbestände die eigene Wettbewerbsfähigkeit erhöht und die dadurch frei gewordene Kapitaldecke anderweitig eingesetzt werden. Es besteht ein enormes Potenzial, wenn man seinen Lagerbestand schlank hält und dadurch die gesamten Lagerhaltungskosten dauerhaft reduziert. Beispielsweise kann durch eine Lagerfinanzierung die Kapitalbindung verringert und das freigesetzte Kapital anderweitig eingesetzt werden. Um die Kostenentwicklung adäquat überwachen zu können, bietet es sich an eine eigene Kennzahl zur Berechnung der Entwicklung sämtlich benötigter Lagerbestände und den dadurch entstehenden Kosten heranzuziehen. Die Kennzahl sollte auf den Betrieb zugeschnitten sein und die jeweiligen Bedürfnisse sowie Bestände beinhalten. In der betreffenden Kennzahl Lagerbestand ist der durchschnittliche Lagerbestand. Die Formel zur Berechnung lautet:
Durchschnitt Lagerbestand = Anfangsbestand + Endbestand/2
Weitere Lagerkostensenkungen können beispielsweise durch verbesserte Einkaufskonditionen erreicht werden. Wenn es anfangs auch mühsam erscheint, kann es sich als lohnend erweisen, sich um die regelmäßige Durchsicht der aktuellen Preise zu kümmern sowie bei den Lieferanten nach Einstandspreisen oder Sonderkonditionen nachzufragen. Der Abschluss von Rahmenverträgen bietet auch den Lieferanten eine gewisse Sicherheit bezüglich der regelmäßigen Abnahme eigener Bestandswaren durch ihren Betrieb.
Gerade durch Rahmenverträge verbessert man die Zusammenarbeit und kann nicht nur die eigenen Kosten durch verbesserte Lieferverträge senken, sondern auch von verkürzten Lieferzeiten profitieren. Mit etwas Geschick ist es sogar möglich kurzfristige Lieferungen je nach Bedarf zu erhalten. Das spart nicht nur bares Geld, sondern wirkt sich auch senkend auf die Lagerhaltungskosten aus. Letztendlich empfiehlt es sich, aufgrund der ausgedünnten Warenbestände sich mit der Versicherung auseinanderzusetzen. Wird nun der Lagerbestand sowie dessen Wert dauerhaft niedrig gehalten, sind Versicherer durchaus geneigt die vorab verhandelten Prämien der neuen Situation anzupassen. Dies sorgt wiederum für Einsparungen.
Just-in-Time-Beschaffungen
Im Just-in-Time-Verfahren, werden benötigte Materialien zum Zeitpunkt des Produktionsbedarfs geliefert und gehört somit zum wertschöpfenden Organisationsprinzip vieler Unternehmenskulturen. Dieser Vorgang schlägt sich durchaus positiv auf die Unternehmensbilanz nieder, da mit Just-in-Time-Beschaffungen geringere Kosten zu erwarten sind. Sie steuern den gesamten Materialfluss derart, dass er zeitlich auf sämtliche Produktionsabläufe abgestimmt ist. Die benötigten Materialien werden erst dann geliefert, wenn ein Produkt von einem Kunden in Auftrag gegeben wird.
Ein Nachteil dieses Verfahrens ist, dass das Unternehmen sich in einer Abhängigkeit zum Lieferanten befindet, was bei Lieferengpässen aufgrund nicht vorrätiger Ware beziehungsweise verkehrstechnischen Problemen zu Lieferausfällen führt. Auch der umfangreiche Kommunikationsaufwand zwischen Lieferant und Abnehmer erweist sich als Nachteil. Um eine ungehinderte Beschaffung von Warenbeständen über Just-in-Time zu beziehen, ist ein elektronischer Datenaustausch zwischen Zulieferer und Abnehmer unausweichlich. Beispielsweise kann sich auch ein kleiner Betrieb für Hüte, die dort in Eigenregie hergestellt werden, für Just-in-Time entscheiden. Der Betriebsinhaber bestellt die benötigten Materialien bei seinem Lieferanten erst dann, wenn er Kundenaufträge für die handgefertigten Hüte erhält.
Technisch aufgerüstet und optimiert – so sieht das Lager der Zukunft aus
Durch Umbaumaßnahmen und Investitionen in modernste Lagertechnik lässt sich nicht nur eine schnellere Kommissionierung erzielen, sondern auch eine deutliche Erweiterung der Gesamtkapazitäten erreichen. Vom Schmalgang-Hochregal bis zum Flach- und Blocklager über SPS gesteuerte Verschieberegalanlagen oder technisch modernste Regalschlitten, die auf Knopfdruck bis zu 190 Tonnen bewegen, vielerlei ist möglich. Und technisch gut ausgerüstete Einfahrregale sorgen unter anderem für eine schnelle Ein- und Auslagerung, mit höchster Umschlagsgeschwindigkeit. Eine weitaus verbesserte logistische Steuerung, die nicht nur eine optimierte Lagerhaltung von Halb- bzw. Fertigerzeugnissen, sondern auch auftragsgebundene oder tägliche Bereitstellungen bestimmter Produktionsmittel bedient. Der so optimierte Materialeingang bis hin zum fertigen Produkt kann verbessert werden und gleichzeitig notwendige Reserven an Lagerkapazitäten schaffen. Das Endprodukt wird letztlich termingerecht und unter besten wirtschaftlichen Bedingungen beim Kunden ausgeliefert.
Auch den Mitarbeitern kommen technische Neuerungen entgegen. Sie können mit vereinfachten Methoden mehrere Behälter in einem Kommissionsdurchlauf bearbeiten. Das System gibt sozusagen vor in welchen Behälter die Ware hinzugefügt wird. Mit den Handscannern wird dann der jeweilige Vorgang der Warenbewegung quittiert. Und um die Kommissionierung von Aufträgen mit Kleinmengen zu beschleunigen, können Sie Bereiche definieren, die das System regelmäßig dazu auffordert eine Neubevorratung zu veranlassen.
Intelligentes Auftragssystem
Das System berücksichtigt unter anderem sämtliche Waren, denen Eilaufträgen zugeführt werden müssen, sowie Waren, die direkt zu einem Unternehmen zwecks Weiterverarbeitung geleitet werden müssen. Dringende Aufträge, die direkt zu einem Weiterverarbeiter gehen, werden entsprechend zugeführt, ebenso wie Waren, die sofort an den Kunden gesendet werden müssen. Neu eingehende Ware wird vom EDV-System erfasst, eventuell umgepackt und dann dem freien Lagerort, den das System vorschlägt, zugeordnet.
Die Kriterien für den Platzvorschlag in einem der Hochregallager sind je nach Kapazität frei wählbar, sodass Großmengen in das automatische Hochregallager transportiert werden. Kleinmengen hingegen kommen ins Kommissionierungslager. Am Ende kommen die Waren nach der Einlagerstation in Behältnisse, die auf die automatische Fördertechnik gestellt werden. Die Kisten wandern nun über die EDV-gesteuerte Anlage in den richtigen Lagerbereich. Der Staplerfahrer setzt die ihm zugeführten Paletten in größeren Mengen auf die Rollenbahn. Von hier aus werden sie nun automatisch gesteuert in dem Hochregallager eingelagert.
Ihr regelmäßiges Update zur Finanzbranche
Erhalten Sie regelmäßig die aktuellsten Meldungen zur Finanzwelt sowie exklusive Tipps und Tricks rund um das Thema Unternehmensfinanzierung.
Ja, ich möchte den FinCompare Newsletter erhalten.
* Pflichtfelder
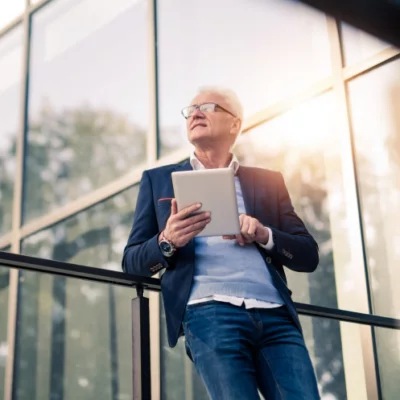